Par Bernard REINTEAU, journaliste spécialisé le 02 Juillet 2020
Organisé mi-mars dernier par le Cetiat et Allice, le forum Fire 2020 a présenté un panel complet des moyens et de l’ingénierie proposés aux industriels pour réduire les émissions de chaleur de leurs activités. Un point essentiel pour favoriser la réindustrialisation.
Où en est le développement des solutions d’efficacité énergétique en industrie ?
Cette question motive le Cetiat et Allice (Alliance industrielle pour la compétitivité et l’efficacité énergétique) depuis de nombreuses années. Le Cetiat anime depuis près de dix ans les colloques Fire – Forum industrie et récupération d’énergie – pour faire le point sur les avancées conceptuelles et techniques sur ce sujet central qui est, par ses aspects environnementaux, indispensable à la relance industrielle en France. La 8e édition s’est tenue mi-mars et a permis d’apprécier l’éventail très large des solutions possibles et à l’étude.
En ouverture du colloque, Youmna Romitti, ingénieure au Cetiat, a brossé les enjeux que représentent les gisements de chaleur fatale : 109,5 TWh annuels. Elle a orienté le regard vers les techniques de récupération de chaleur sur les buées des séchoirs qui représentent 27% des rejets, soit près de 30 TWh (voir la figure n° 1). La moitié de cette ressource est de moins de 100°C ; l’autre moitié affiche une température de plus de 100°C, parfois de plus de 200°C en biscuiterie et boulangerie.
- Figure N°1 - Gisement de chaleur fatale -
- Origine du gisement de chaleur fatale : L'industrie agroalimentaire est aujourd'hui le premier émetteur de chaleur fatale -
Des développements sur mesure
L’étude qu’elle a menée pour Allice a porté sur les différentes solutions de valorisation des buées de fours applicables à l’industrie agro-alimentaire afin d’apprécier leurs arguments technico-économiques.
Premier exemple dans une biscuiterie. Les buées à 192°C d’un débit de 1,5 t/h traversent un premier échangeur de 42 kW qui permet de porter l’air introduit directement dans la chaudière de 20 à 120°C. Un second échangeur-condenseur peut être placé sur le conduit d’extraction des buées pour exploiter le solde de température ramenée à environ 90°C et préchauffer de l’eau nécessaire à la production industrielle ; l’eau froide peut ainsi être portée à près de 50°C (voir la figure n° 2). Un tel montage demande un investissement estimé entre 30 000 et 90 000 € et peut produire un retour sur investissement brut en 3,5 ans.
- Figure N°2 - L'installation de deux récupérateurs sur la cheminée du four réduit les consommations d'énergie pour la cuisson et la production d'eau chaude -
La réduction des dépenses de combustible gaz peut atteindre 15 à 35%. Plusieurs fournisseurs d’échangeurs à tubes lisses ou ailettés sont déjà présents sur le marché. Elle cite notamment les productions de la société Ecopôle
Pour sa part, Julien Caizergues, responsable du développement du marché Industrie chez le breton ETT a présenté deux solutions dont les retours sur investissement se sont avérés rapides :
1. un récupérateur dans une usine de thermoformage qui reprend les calories de l’air extrait pour préchauffer l’air neuf par batterie d’eau chaude en amont de celle alimentée par une chaudière de 63 kW : l’unité d’une capacité de 33 000 m³/h d’un coût de 75 000 € est annoncée avec un retour sur investissement immédiat ;
2. un récupérateur placé en sortie d’étuve d’un débit d’air de 17 600 m³/h à 55°C alimente une batterie hydraulique dans le caisson de soufflage d’air neuf d’une cabine de peinture et, en hiver, préchauffe les 28 000 m³/h à 22°C ; l’investissement de 35 000 € est amorti en 11 mois.
Intégrer la récupération d’énergie dès la conception
Youmna Romitti souligne qu’il vaut mieux intégrer ces solutions dès la conception des lignes de production. Elle indique qu’il est impératif de les monitorer et de veiller à leur maintenance – l’une des contraintes de la récupération est l’encrassement lié au transport des effluents chargés (voir la figure 3). Selon les productions, il est possible d’utiliser des échangeurs tubulaires (du type Alfa Laval), rotatif (du type Trianon d’ETT), ou caloduc (disponibles chez ETT, Spirax Sarco …).
- Figure N°3 - La chaleur fatale industrielle par région : Les régions industrielles historiques sont toujours fortement représentées au palmarès des émissions.
La Bretagne, très équipée en industries agroalimentaires à partir des années 50, se distingue aussi -
Autre solution étudiée depuis maintenant plusieurs années : l’utilisation des buées de séchage comme source froide pour une pompe à chaleur capable de produire une eau de très haute température : 150°C ou plus.
Quelques sites industriels en Europe exploitent déjà cette technologie. Il s’agit de deux laiteries, Arla Rinco au Danemark et Frieslandcampina aux Pays-Bas ; le troisième est le séchoir d’une tuilerie-briquèterie Wienerberger en Autriche. Ce dernier est mené avec la Cnim (voir l’encadré à ce sujet). Ce sujet semble d’un intérêt particulier puisque trois projets européens sont dans les starting-blocks : la PAC Transpac mise au point par EDF R&D qui doit être testée chez un papetier (le lancement du projet remonte à une dizaine d’années et figurait parmi les exposés des premières conférences Fire), le projet européen DryFicency mené par le consortium AIT sur trois sites industriels (https://dry-f.eu/Industrial-heat-pumps/Open-loop), et un projet GEA Réfrigération.
Youmna Romitti souligne à la fois le potentiel de ces travaux de R&D et les développements encore nécessaires.
Elle pointe notamment :
— l’amélioration des systèmes d’extraction afin de confiner et réduire les débits d’air de dilution induits pour mieux exploiter ce gisement ;
— le déploiement de l’instrumentation des séchoirs pour réguler les débits d’extraction selon divers critères (humidité, débits …) ;
— la mise au point de solution de financement pour l’équipement de l’industrie, par exemple sur la base des certificats d’économie d’énergie.
Livrer l’énergie à la collectivité
Jean-Jacques Lebatard, co-fondateur et responsable de la nouvelle société Evertgie, présente les technologies et les modalités de calculs économiques que son entreprise propose à ses clients. Ses solutions d’exploitation de la chaleur fatale reposent essentiellement sur des pompes à chaleur de haute et très haute température, c’est-à-dire capable de fournir une eau de plus de 95°C.
S’adressant aux industries de la chimie, de l’agro-alimentaire ou du chauffage urbain, il retient des équipements de grandes puissances – plus de 500 kW – et capable de recevoir une source froide d’un niveau de température déjà élevé – de 20 à 100°C. Pour améliorer les rendements, les choix techniques l’orientent généralement vers des solutions de pompes à chaleur en cascade.
Jean-Jacques Lebatard donne en exemple du réseau urbain de Maisons-Alfort (Val de Marne) qui reçoit une partie de la chaleur de l’entreprise Bio-Springer, fabricant de levures. Avant rejet en Seine à une température de 18°C, les effluents chauds alimentent une pompe à chaleur d’une capacité de 1,74 MWh thermique d’un coefficient de performance de 3,2 qui produit une eau à 85°C.
Autre exemple à Dijon où Evertgie a conçu la solution de récupération de la chaleur émise par un datacenter : la pompe à chaleur d’une capacité de 433 kWh thermique (cop de 2,5) rejette, côté évaporateur, de l’eau à 10°C pour climatiser l’installation informatique, et, côté condenseur, de l’eau à 95°C qui est livrée au réseau de chaleur urbain.
Fort de son expérience, ce maître d’œuvre livre quelques points incontournables pour analyser ce type de projet. Ainsi, plutôt que de limiter l’étude financière au délai de retour sur investissement qui prend seulement en compte la valeur de l’investissement sur l’économie réalisée, il suggère une analyse financière plus complète, dite taux de rendement interne (dit TRI), qui compile les paramètres de la dépréciation annuelle de l’équipement au regard de la durée d’amortissement de l’investissement, les économies produites et les flux de trésorerie engendrés. Ces indicateurs lui semblent plus adaptés à la démarche de valorisation énergétique.
Par ailleurs, pour ce qui concerne l’appréciation du cycle de vie de l’installation de récupération, il invite les investisseurs à ne rien négliger dans leur analyse. Il cite les critères :
– l’énergie consommée, en kWh,
– l’appréciation de l’empreinte carbone sur la base du Tewi (« total equivalent warming impact », que l’on peut traduire par « impact de réchauffement équivalent total ») exprimé en tonne de dioxyde de carbone (tCO2) ;
– les consommations électriques et les fuites de fluides (en moyenne annuelle à 10-15% du volume chargé) ;
- les coûts de maintenance.
Tirer profit de toutes les solutions de stockage
Les experts en thermodynamique n’ignorent rien des solutions physiques de stockage de la chaleur. Chercheur au département « Thermique, biomasse et hydrogène » du CEA-Liten (Laboratoire d’innovation des énergies nouvelles et les nanomatériaux du Commissariat à l’énergie atomique), Jean-François Fourmigué rappelle les trois types de chaleur connus et exploitables pour le stockage :
– la chaleur sensible, liée à l’élévation de température d’un solide ou d’un liquide ;
– la chaleur latente, liée au changement de phase, par exemple solide vers liquide ;
– la chaleur de réaction, provoquée par une réaction chimique réversible, qu’elle soit endo ou exothermique.
Son exposé lors du dernier congrès Fire a éclairé l’assistance sur les possibilités de stockage dans les trois cas de figure.
La chaleur sensible peut être stockée dans des liquides ou des matériaux solides.
Parmi les liquides, il détaille :
– l’eau, jusqu’à 80°C : c’est généralement la solution retenue en aval de capteurs solaires thermiques ;
– des huiles thermiques sans pression – pour des températures jusqu’à 300°C – ou sous pression – jusqu’à 400°C ;
– des sels fondus (fluorure, chlorure ou nitrate) pour des températures de 550°C, voire plus ...
Parmi les matériaux solides, il cite des solutions très diverses qui ont déjà fait l’objet de thèses et de travaux de recherches : les sols à l’aide de pieux géothermiques, des lits de roches artificiels, des cylindres de béton comme ceux proposés par EnergyNest ou des matériaux céramiques. Il est ainsi possible de stocker, pour des cycles courts ou inter saisonniers, des températures de 600 à 800°C. Ces solutions servent à alimenter des réseaux de chaleur, des installations de production d’électricité …
C’est d’ailleurs la solution technique revendiquée par l’entreprise ID Helio qui présentait lors de ce congrès une installation solaire de production de chaleur pour le séchage et la pasteurisation de fruit pour l’entreprise Fruit Gourmet dans le Lot-et-Garonne. Une ombrière couverte de concentrateurs solaires à miroirs de Fresnel produit une chaleur de 250°C. Elle est stockée, par un flux d’air, dans un conteneur chargé d’un mélange de calcaire, de granit et de Cofalit, un matériau issu de la vitrification de l’amiante par torche à plasma.
Les applications de ce stockage sont multiples et, souligne Jean-François Fourmiqué, elles s’appliquent parfaitement aux industries qui cherchent à récupérer les énergies fatales. Parmi elles, l’exploitation du changement de phase des matériaux parait le plus intéressant, notamment en raison des régimes de température adaptés aux activités. Ainsi, les matériaux organiques – paraffine ou alcools de sucre – conviennent pour des niveaux de 20 à 200°C ; des hydrates de sels peuvent servir aux mêmes usages jusqu’à 200°C, des sels, jusqu’à 400°C.
Les avantages connus sont principalement la densité de stockage élevée sans écart de température important, une décharge à température constante – en fonction de la température de solidification du matériau – et une adaptation aux fluides de transfert diphasique. Parmi les usages en cours, ce chercheur cite le stockage de chaleur dans une sous-station du réseau de chaleur de Grenoble dans le cadre de l’opération CityZen. Les matériaux à changement de phase fondent à 70°C et assurent une puissance de 180 kWh.
Pour ce qui concerne le stockage thermochimique, le CEA Liten travaille aussi sur les capacités de la chaux vive ou de la chaux éteinte. Soumise aux cycles d’hydratation et de déshydratation, il est possible de la charger en températures de 350 à 500°C.
Un autre travail en cours – en logement individuel et non sur l’industrie – porte sur les propriétés du bromure de strontium (voir la figure 4). Le réservoir contenant une charge de 8 t et placée sous terre sur le trajet d’un puits canadien emmagasine les calories de l’air. Il les restitue via un échangeur pour préchauffer l’eau chaude sanitaire. Les tests menés sur une maison solaire témoin du site du CEA à Grenoble fait apparaître un potentiel de couverture des besoins annuels de l’ordre de 80%. La solution serait transposable à l’industrie.
- Figure N°4 - Le stockage thermique individuel -
Quel bilan tirer de cette édition 2020 du congrès Fire ?
L’ingénierie et les technologies de valorisation énergétique ont connu, au cours des dix dernières années, une évolution manifeste.
Leur intégration aux sites existants ou à créer paraît désormais une évidence. À tel point qu’elles doivent permettre à l’industrie de se présenter comme énergétiquement efficiente au moment où verdissement des activités et réindustrialisation sont au cœur des débats.
- Le Forum Fire 2020, organisé par le Cetiat et Allice mi-mars dernier, a réuni les ingénieurs et industriels les plus en pointe sur l’exploitation de la chaleur fatale en industrie -
Exemple 1 – La Cnim adapte la pompe à chaleur à absorption à la récupération de chaleur fatale
L’entreprise française a développé une PAC à absorption pour l’usine autrichienne de thermo briques Wienerberger. Le module installé dans un conteneur exploite la chaleur extraite du four et les buées du tunnel de séchage des briques pour fournir un air préchauffé pour le four et le tunnel de cuisson.
Le 1er briquetier mondial et 1er tuilier européen Wienerberger se préoccupe d’efficacité énergétique de son process de production. Deux points de perte d’énergie sont plus particulièrement ciblés : le four de cuisson d’où sont extraits des fumées à 400°C, pour une puissance de 700 kW ; et le laveur des buées en sortie du tunnel de séchage des briques d’où peut être extrait un air à 39°C pour une puissance de 500 kW. Il faut noter que, comme dans toute industrie de la terre cuite, la chaleur du four était déjà exploitée pour alimenter le tunnel de séchage.
Comment optimiser l’exploitation de ces calories ? L’idée apportée par la Cnim, a indiqué Alain Guinot dans son exposé lors de Fire 2020, est d’alimenter une pompe à chaleur à absorption au bromure de lithium avec ces flux pour restituer intégralement cette énergie. Avantage supplémentaire : une partie de la chaleur pourra être renvoyée pour préchauffer le four de cuisson et l’autre vers le tunnel de séchage.
L’intérêt d’une telle application est aussi de la confronter à une situation industrielle. Car un tel type de PAC est connu pour fonctionner correctement sans variation des conditions de fonctionnement. Cependant, cette usine montre des fluctuations d’énergie liées aux cycles de fabrication, à la température ambiante … Si l’hypothèse reste intéressante, la régulation de la PAC doit être modifiée pour s’adapter aux variations rencontrées, et le pilotage de la PAC doit éviter la cristallisation du bromure de lithium. Lors de cette présentation, Cnim annonçait que les évaluations d’économies de gaz étaient en cours.
- La pompe à chaleur à absorption au bromure de lithium reprend les fumées du four au niveau du générateur et les calories issues du lavage des buées de séchage au niveau de l’évaporateur. L’énergie restituée préchauffe l’air du four et du tunnel de séchage -
Exemple 2 - Un module et un ballon pour tirer profit des groupes frigorifiques
Pour les spécialistes de thermodynamique, exploiter la désurchauffe sur les groupes de froid est déjà chose connue. L’entreprise Boostherm prend le risque d’aller plus loin en exploitant la totalité de la chaleur disponible de la phase de condensation. Ses modules sont parés d’une régulation robuste.
Comme l’explique l’entreprise Boostherm, intercaler un récupérateur de calorie entre les compresseurs d’une installation frigorifique et le condenseur à air n’a rien d’une nouveauté. En industrie agroalimentaire (abattoir…) et en commerce, l’intérêt est évidemment d’utiliser l’énergie chèrement produite pour les chambres froides pour chauffer l’eau chaude sanitaire ou alimenter le chauffage dont on a forcément besoin sur le site.
Généralement, seule la désurchauffe est exploitée, soit 15 à 20% de l’énergie fatale disponible. Le reste repasse par le condenseur à air de manière à ne pas trop perturber le cycle thermodynamique. L’innovation apportée par Boostherm exploite la quasi-totalité de cette chaleur en sortie de compresseurs pour optimiser le rendement.
Ainsi, quel que soit le type de fluide frigorigène exploité classiquement dans les installations de froid* – qu’il s’agisse de réfrigération (froid positif) ou de congélation (froid négatif) –, ce fournisseur propose aux exploitants de compléter leur local technique de deux éléments : un module de récupération de chaleur et un ballon spécifiquement conçu pour le stockage, le transfert et la production d’eau chaude.
* Compléter l’installation avec récupérateur et ballon
Le récupérateur comprend essentiellement trois sous-ensembles :
— un échangeur à plaques adapté au passage des fluides frigorigène pour un transfert de chaleur à l’eau en circulation à contre-courant – à deux plaques de séparation pour éviter les risques liés aux fuites (gardons à l’esprit que certains fluides frigorigènes sont à pratiquement 40 bar en sortie de compresseur…) ;
— une pompe à vitesse variable entre le ballon et l’échangeur ;
— une régulation pour gérer l’échange thermique en fonction du potentiel et pour éviter certains risques, comme le défaut de fluide en cas de fuite ou la protection contre le gel entre l’échangeur et le ballon.
Ces modules sont disponibles en puissances de 5 à 600 kW. Un simulateur en ligne** permet de retenir le modèle selon plusieurs critères : la puissance thermique du condenseur, l’application (réfrigération négative ou positive, fluide, le volume d’eau chauffée pour répondre aux besoins de chauffage et d’eau chaude sanitaire …) ; cet outil d’aide à la décision fournit aussi une estimation du retour sur investissement.
Second équipement essentiel à ce complément d’installation : le ballon. Boostherm a développé un large catalogue de modèles pour répondre à pratiquement tous les cas de figures :
— des ballons combinés pour le stockage d’eau préchauffée et la préparation d’eau chaude sanitaire : de 300 à 5 000 l, ils sont produits en acier thermolaqué ou en Inox 316L et isolés ; ils présentent de multiples piquages pour augmenter leur éventail d’usages (ECS, chauffage haute ou basse température) ;
— des ballons dits « tank in tank » (ou bain-marie) de 400 à 2 000 l pour un usage ECS et chauffage (1 600 l pour le chauffage et 400 l pour l’ECS dans le cas d’un 2 000 l) ;
— des ballons tampon primaire de 500 à 3 000 l ;
— des ballons de 300 à 3 000 l, avec réchauffeurs de type serpentin en bas de ballon, plus une résistance électrique d’appoint ...
À cela s’ajoute des préchauffeurs à échangeurs à plaques de 50 à 600 kW à placer en aval des ballons.
* Produire une eau chaude à 55°C
L’hydraulique développée par Boostherm consiste à soumettre directement l’eau froide à la chaleur latente de la condensation (voir le principe et les exemples de déclinaisons dans la première figure ci-dessous). L’énergie récupérée permet de porter l’eau dans le ballon à 45-55°C en un seul passage.
Dès que le cycle « condensation à eau » a préchauffé le contenu du ballon et ne permet plus de condenser le fluide frigorigène, la régulation bascule alors en mode « désurchauffeur » : le passage du fluide d’une température de 90 à 45°C peut alors porter le contenu du ballon à 55-65°C, voire plus.
L’intérêt de bypasser la chaleur en sortie de compresseur est multiple. Boostherm argumente en premier lieu en soulignant le court délai entre la sortie de fluide du compresseur et la disponibilité d’eau chaude à une température relativement élevée et directement exploitable en chauffage ou en consommation d’eau chaude sanitaire.
En deuxième lieu, correctement dimensionné, ce « captage d’énergie » ne modifie pas les performances de fonctionnement de l’installation de froid.
Enfin, s’il est nécessaire d’augmenter la pression du fluide pour compenser la perte de charge liée au passage dans l’échangeur à plaques, cela produit certes une surconsommation du compresseur, avoue Boostherm, mais cette dépense supplémentaire est récupérée en chaleur. Et globalement, le coefficient de performance dit « global » - c’est-à-dire, qui tient compte de la production de froid et de la récupération de chaleur au regard de la consommation d’énergie – s’en retrouve amélioré et lissé pendant toute la durée de fonctionnement de l’installation.
L’offre de cet industriel semble séduire les prospects, puisque le catalogue s’enrichit. Aux ballons et préchauffeurs, il rajoute une gamme d’appareils de chauffage pour les surfaces commerciales tels que des aérothermes (muraux standards ou plafonniers déstratificateurs), des cassettes plafonnières, des ventilo-convecteurs, des rideaux d’air…
Le système Boostherm est conçu pour travailler avec les fluides R-22, R-134a, R-404A, R-407A, R-407C, R-407F, R-410A, R-450A, R-452A, R-448A, R-449A, R-513A.
- La solution Boostherm s’adapte à de multiples besoins de valorisation énergétiques -
- La récupération d’énergie en sortie haute pression des compresseurs est optimale -
Exemple 3 - Produire de l’électricité avec la vapeur fatale
La jeune Hevatech, créée en 2010, propose une technologie thermodynamique pour exploiter la vapeur perdue. Un concentré de technologies validées et maîtrisées.
C’est un concentré de technologies connues, éparses et pertinentes. Les ingénieurs peuvent les imaginer bien rangées sur l’étagère. Côte à côte, ils trouvent des échangeurs, un hydroéjecteur, une turbine à augets de type Pelton (très utilisée en petite et grande hydraulique), un alternateur de production d’électricité, un condenseur et des pompes, un fluide minéral caloporteur. Rien que du très classique.
L’idée d’Hevatech a été de rassembler tous ces équipements pour former sa technologie Turbosol destinée à transformer la chaleur perdue de haute température telle la vapeur à 300°C ou plus en énergie.
La boucle thermodynamique (voir la figure « Turbosol schéma de principe ») mise au point commence par un échangeur placé dans la canalisation de rejet de vapeur chargé d’un fluide caloporteur. Ce fluide chaud et mis en pression par une pompe est envoyé à l’une des deux entrées d’un hydroéjecteur ; l’autre entrée reçoit le fluide froid de retour de la boucle thermodynamique.
- La solution Turbosol d’Hevatech rassemble une suite d’équipements classiques pour former un équipement innovant de récupération de chaleur et de production d’électricité -
Ce mélange diphasique et chaud (120°C) est introduit dans l’accélérateur de l’hydroéjecteur qui subit alors une double dynamique : un effet venturi lié à l’entraînement d’un fluide par l’autre, et une accélération du flux dans un cône selon le principe de Bernoulli – la baisse de pression liée à l’augmentation progressive du diamètre provoque une accélération de la vitesse du fluide, équilibre débit/pression oblige. Le jet sous pression, réparti sur plusieurs sorties de l’hydroéjecteur, est alors projeté sur les augets d’une roue de turbine, dite Pelton, qui entraîne un alternateur. Hevatech en propose deux gammes : les TSV1 de 20 à 80 kWe et les TSV2 de 80 à 200 kWe, l’addition des modules pouvant atteindre 1 MWe. En sortie de turbine, eau et huile sont séparées par décantation. L’eau est refroidie par un condenseur avant de traverser un échangeur placé dans la cheminée d’évacuation de la vapeur, puis de revenir en entrée d’hydroéjecteur. La boucle est bouclée.
Multi-primée depuis qu’elle a été lauréate, en 2013, d’un appel à manifestation d’intérêt (AMI) « efficacité énergétique dans l’industrie », organisé par l’ADEME et TOTAL, cette technologie est proposée aux activités liées aux déchets, à la biomasse, à l’industrie lourde, à l’exploitation de groupes électrogènes … L’entreprise drômoise argumente sur les faibles coûts d’investissement, le fonctionnement sûr (fluides à basse pression, vitesse de rotation de la turbine…). Elle offre aussi la possibilité de réaliser de la cogénération sur certains sites : de la chaleur, du froid et de l’électricité.
Voir aussi la vidéo Turbosol
Exemple 4 - Usine Sodéleg / Aisne - La maîtrise des consommations d’énergie participe à la réduction des nuisances du site
Quatre mois par an, l’usine Sodéleg d’Athies-sous-Laon (Aisne) produit 80 000 t d’oignons et échalotes séchés. Cette activité gourmande en énergie émet localement de grandes quantités de composés organiques volatiles (COV) … et d’odeurs. Après audit énergétique du Cetiat en 2017, Clauger a été missionné pour équiper cette chaîne de production d’une récupération d’énergie des fours pour économiser 10% de l’énergie, et réduire les nuisances. Sodéleg souhaitait un projet techniquement exigent permettant de bénéficier du fonds Chaleur.
Construite en 1984, l’unité de déshydratation Sodéleg d’Athies-sous-Laon (Aisne) réalise chaque année, d’Août à Novembre, ses campagnes de traitement des oignons et échalotes récoltés localement. Durant ces 3 000 heures, à raison de 600 t par jour, elle produit 80 000 t de condiments destinés à être intégrer dans les diverses préparations de l’industrie agro-alimentaire. Cette entreprise est leader européen et 4ème mondial sur son secteur.
Si elle a déjà travaillé à réduire ses nuisances et consommations de toute sorte – le site est neutre en eau et il a réduit ses émissions de CO2 de 5 000 t/an –, l’entreprise a souhaité en 2017 poursuivre un plan de progrès visant à baisser les consommations d’énergie de 10% et améliorer son intégration environnementale en réduisant les émissions d’odeurs et de COV.
* Un installation au gaz naturel … qui libère des COV méthaniques
L’activité la plus énergétiquement intense se concentre sur une ligne de trois équipements alimentés au gaz naturel :
– un préchauffeur d’une puissance de 1,5 MW qui fonctionne sur le principe d’une production de vapeur – 100 000 m³/h – pour provoquer un choc thermique bactérien ; cette phase produit des rejets importants, bruyants, dont l’odeur porte jusqu’à 40 km et qui contiennent les COV méthaniques (du CH4) relargués par les bulbes ;
– un four dit « 77 » – nommé ainsi en raison de son année de construction – d’une puissance de près de 10 GW et qui assure la déshydratation des produits de 82 à 10% d’humidité ; le traitement d’environ 2 heures produit une évaporation de 350 000 m³/h d’une vapeur très chargée en matière sèche ;
- un four dit « 86 » qui abaisse l’humidité des produits traités de 10 à 4,5% par un process d’environ 4 h 30 ; les rejets des vapeurs sont de 64 000 m³/h.
* Exploiter les rejets du préchauffeur
L’analyse du site fait apparaître :
- que les principales nuisances se situent au niveau des rejets du préchauffeur ;
- et que le four le plus ancien, le « 77 », est le plus gourmand en énergie.
Celui de « 86 » présentait un moindre potentiel de gains.
Pour autant, Clauger a souhaité disposer de solides données de fonctionnement avant de lancer son bureau d’études sur une solution du problème posé. Car l’enjeu est de taille : le rendement de la solution doit être maximal, et l’installation doit présenter une fiabilité totale pour une disponibilité sans faille durant les quatre mois de campagne. Et pour bénéficier du fonds Chaleur, le projet d’aménagement devait répondre à trois critères : avoir fait l’objet d’une étude de faisabilité ; valoriser une ressource non encore valorisée et la restituer sur un autre procédé ; atteindre un seuil de valorisation d’énergie thermique de plus de 1 GWh/an. L’aide serait alors d’au moins 30%.
En premier lieu, Clauger a obtenu de son client un audit complet sur une saison, avec l’ensemble des données d’exploitations. Cette entreprise a aussi pu poser des capteurs de toutes sortes (quantité de vapeur, pression en jeu, températures, humidité …) ; les résultats ont été transmis via un concentrateur.
En second lieu, ce concepteur-installateur a préparé son intervention en effectuant 60 scans du bâtiment de l’usine, d’une précision millimétrique. Ces nuages de points ont permis de créer une maquette numérique de son projet.
* Transférer les rejets du préchauffeur sur le four
La solution retenue par Clauger est centrée sur le préchauffeur et le « four 77 ».
1- Les 100 000 m³h de rejets de ce premier traitement sont intégralement captés pour être transférés vers quatre condenseurs cycloniques d’une capacité de 25 000 m³/h chacun. Cette étape permet de séparer ce flux : les matières sèches ainsi que les condensats (95% d’humidité relative) sont récupérés ; et 12 km d’échangeur en tube d’inox captent la chaleur (environ 36°C) sur cet air propre et sec.
2. L’air sec chargé en COV et en méthane est conduit vers une centrale de traitement d’air. Dimensionnée pour 135 000 m³/h, elle reçoit les 100 000 m³/h des cyclones et 35 000 m³/h d’air extérieur.
Elle est équipée d’une batterie chaude de 1 170 kW et de 4 600 m² de surface d’échange en inox/aluminium/magnésium – air corrosif oblige –, alimentée par un groupe thermodynamique à deux compresseurs ; sa source froide est reliée aux échangeurs des condenseurs cycloniques – le régime est de l’ordre 16-17°C en entrée de PAC et de 10-11°C en retour (voir la figure correspondante).
- La préparation du chantier d’installation de la récupération d’énergie a commencé par une campagne de mesure et la création d’une maquette numérique des bâtiments industriels -
- L’installation valorise l’important gisement de chaleur issu du préchauffage. La solution permet non seulement de réduire les consommations d’énergie mais aussi les nuisances olfactives et sonores de l’usine -
Cette pompe à chaleur produit une eau à 42-50°C et affiche un Cop de 4. Le régime de température est d’environ 48°C en départ de PAC et de 38-39°C en retour de la batterie chaude.
3. L’air est intégralement introduit dans le four de déshydratation « 77 » à 45-50°C. Les COV méthaniques (du CH4), à raison de 18 kg/h, sont consommés comme air comburant par les six brûleurs.
* Des consommations de gaz fortement réduites
Alors qu’initialement le four 77 recevait un air à 17°C et à 70% HR, cette installation a totalement modifié les conditions de fonctionnement. L’air introduit est désormais à 49°C et à 22% HR, soit une puissance thermique « gratuite » apportée de 1 800 kW. À lui seul, le méthane (CH4) contenu dans l’effluent (330 mg/Nm³) assure quelques 428 kWh. Le pilotage du four serait même amélioré par la régularité de la température du flux d’air entrant.
Les résultats s’avèrent concrètement meilleurs qu’attendus. Les gains énergétiques comptabilisés lors de la campagne 2019 atteignent 6,65 GWh pour une estimation de 5,4 GWh. Il en va de même pour les émissions de CO2 (-1 556 tCO2), les émissions méthaniques, les odeurs (-27% des unités d’odeur – UOE – par m³). La baisse du niveau sonore contribue aussi à l’acceptabilité locale du site industriel.
Pour l’entreprise Clauger, cette intervention a nécessité six mois d’études de conception et deux mois de chantier. Le marché comprend aussi un accompagnement de l’industriel pour l’exploitation et le suivi du site durant six ans.
Financer la performance énergétique en industrie - Utiliser les C2E et le fonds Chaleur
L’aide aux sites industriels pour la mise en place de solutions techniques de réduction des consommations d’énergie a évolué, fin 2019. Ainsi, les sites soumis à quotas d’émission de carbone, dits « EU ETS » et , peuvent, depuis la parution de l’arrêté du 20 Septembre 2019*, bénéficier de certificats d’économie d’énergie (CEE). Cette mesure pour les sites très consommateurs d’énergie pouvant présenter un certificat de management énergétique ISO 50001 est d’ailleurs rétroactive au 1er Janvier 2019.
D’autre part, depuis Août 2019, les sites qui valorisent plus de 12 GWh/an d’énergie peuvent bénéficier d’une aide par certificats d’économies d’énergie (CEE) et du fonds Chaleur. Cette dérogation ne vaut que pour quelques fiches standardisées d’opération (BAR-TH-137 et BAT-TH-127, et RES-CH-108 avec un dossier spécifique en raison de sa limitation théorique à 12 GWh/an). L’aide du fonds Chaleur tient compte de l’aide CEE sur une base de 5,5 €/MWh cumac.
Les aides à la récupération de la chaleur fatale ont aussi évolué. Si la solution exploite un système thermodynamique, les valorisations d’un niveau inférieur à 6 GWh/an peuvent bénéficier d’une articulation CEE – fonds Chaleur. Pour ce qui concerne la valorisation supérieure à ce seuil de 6 GWh/an, l’aide CEE plus fonds Chaleur s’étudie systématiquement sur la base d’une analyse économique.
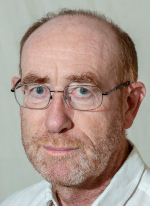
À propos de l'auteur
Bernard Reinteau
Journaliste de la presse bâtiment depuis la fin des années 80, Bernard Reinteau est journaliste indépendant. Il a œuvré pour les principaux titres de la filière et se spécialise particulièrement sur les solutions techniques liées à la performance énergétique et environnementale des constructions et rénovations performantes. Il collabore principalement avec les plus grands titres et en particulier avec Xpair.